M
Articles/News
Since our founding in 1995, we have specialized in flow control
and valve automation with an unwavering Vision.
Home |
How Valve Actuators Can Help Improve Process Control
Valve actuators can be the difference between process failure and success. This is because no matter what your process objective is, flow rates have to be controlled at a number of points throughout the process.
Variables such as temperature, pressure, tank levels, flow and more must be closely regulated in order to achieve the desired outcome. And it must do this as well as maintain operating reliability and safety.
The control valve is the one that physically controls the process media, but it is the actuator which is the brains, and the heart, of the operation. This is why the valve actuators are vital: they provide important process control.
5 considerations for specifying a valve actuator
Deciding on which valve actuators are necessary should be an early part of the design process. There are six considerations to be made by design engineers to help guide the specification process.
Each consideration is really more a series of questions about what’s needed for process control, energy requirements, as well as environmental considerations.
The 5 considerations are:
-
Control objectives
Does your process have much tolerance for variation? The precision and repeatability of the actuator play a necessary role.
Is the work of the actuator continuous or intermittent? If an actuator has duty-cycle limitations it can trip out and overheat if it’s frequently stopped and started. Also, dead bands that are used to limit modulation are sometimes too wide to provide adequate resolution for the necessary control
For constant control requests, you want actuators capable of continuous modulation for a better resolution.
-
Cost and power availability
Cost is an obvious consideration. Most businesses want to run as efficiently as possible; not only to save money, but also to meet their environmental sustainability targets. Which is why you need to consider the amount of energy devoted to running an actuator.
High-voltage electric actuators require more energy and depending on whether you use one-phase or three-phase lines, it can be a costly endeavor.
However, if you’re considering pneumatic infrastructure, it’s even more expensive to run and support this than electric.
Depending on your situation, it may be ideal to look at newer electric actuators that run on 12 volts. These can be installed remotely and can be powered by fuel cells or solar panels. An added advantage of this is backup power becomes economical because of the lower power requirements.
-
Type of valves
Does the process need linear or rotary quarter-turn valves? The right valve type for a particular application is really its own science. Once you have decided on the appropriate valve type, then you can consider the best style of the actuator for your process.
-
Actuator sizing
Which type of valves need to used? And what is the required force to actuate them? An oversized actuator can cause damage to the valve stem, while an undersized valve might not be capable of operating the valves required thrust or torque.
This is why it’s important to know the current valve and require force. Irrespective of the mounting approach of a valve, actuators that are of the wrong size can cause poor valve control.
-
Environmental conditions
There are two broad categories of environmental conditions you should consider. Environmental safety and operation conditions.
For operation conditions: what range of ambient temperature is expected? And is the actuator going to be subject to submersion or exposed to severe weather extremes? Is the actuator’s rated temperature range and enclosure certification suitable for the environment? These are vital considerations as only certain actuators can operate in certain conditions.
For safety conditions: if there are explosive dust or gases present you must choose an actuator with the appropriate Class and Division certifications.
How ATI Actuators can help improve the control process
The right actuator has a substantial impact of safety, process quality, energy consumption, productivity, the environment, and equipment life.
This is why you need to consider all of your actuator choices early on in the process. Especially where process control performance is a factor.
You also want to work with an established, reputable company who can design and manufacture valve actuators for customized applications to your exact specifications.
If you have any questions, or would like to know more about who actuators can help improve the control process, please contact us today.
FAQ:
1. What is the significance of valves in process control?
Valves play an important role in process control, as they offer stability in almost all of the applications. In addition to helping in better control of flow, valves also ensure enhanced regulation of pressure and temperature. All of these aspects combined, enable the process to continue for a considerably long period of time, without any potential risks or failure. Not only does it ensure the efficiency of the process, but also adds an element of cost-effectiveness to the same.
2. What is the purpose of using actuators in industrial setups?
In industries, actuators serve many purposes including but not limited to operating valves, valves, dampers, fluid couplings, and other devices. Simply put, actuators facilitate industrial process control. Depending on the preferred source of power, industries can use Pneumatic, Hydraulic or Electric Actuators.
3. Which actuator is best for control valve?
In case of ready availability of electricity, electric actuators can serve the purpose fairly well. However, if regular power supply is an issue pneumatic or hydraulic valve actuator can be taken into consideration. That said, it must be noted that pneumatic actuators require an air supply ranging between 40 and 120 psi.
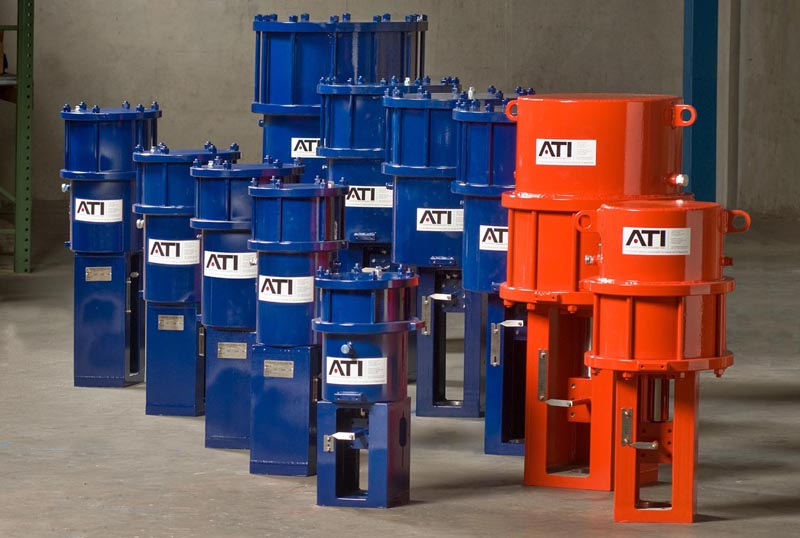