M
Frontline Services
ATI adds value to our Valve Automation offerings through our specialized maintenance service group.
Home |
Field Installation Services
ATI FrontLine Services, the company’s specialized maintenance service group, operates from the new facility as well. The team offers expert field and in-house valve actuator repair, retrofitting, refurbishment, and replacement as well as automation calibration.
The combination of all products and services at our facility ensures that our clients are provided with a high level of customer service, increased efficiency, improved quality, and decreased delivery times. After all, no one knows an ATI actuator better than we do. We designed and manufactured it from day one. Our services include retrofits, safety system calibrations, and installations at the job site. Repairs include:
- Complete disassembly for audit
- Thorough inspection and cleaning
- Stocked parts including seals and gaskets
- Machining and parts replacement as needed
- Re-assembly to strict ATI standards
- Complete final pressure and operation testing
- Paint
Rebuild and Retrofit
We have the experience to retrofit ATI and other actuator brands to extend their performance. We offer bolt-on kits to update Shafer, EIM, and other valve actuator brands without removing them from service. Among other items, ATI can replace hand pumps, high-pressure controls, limit switches, and poppet blocks.
01. Retrofit Services
ATI FrontLine Retrofit Services can provide:
- Easy field change out with retrofit packages
- Parts and materials in stock
- ATI-engineered and fabricated brackets
- Pre-assembled panels
- Retrofit with an existing pneumatic, hydraulic, gas-over-oil, or electro-hydraulic system
02. Calibration Services
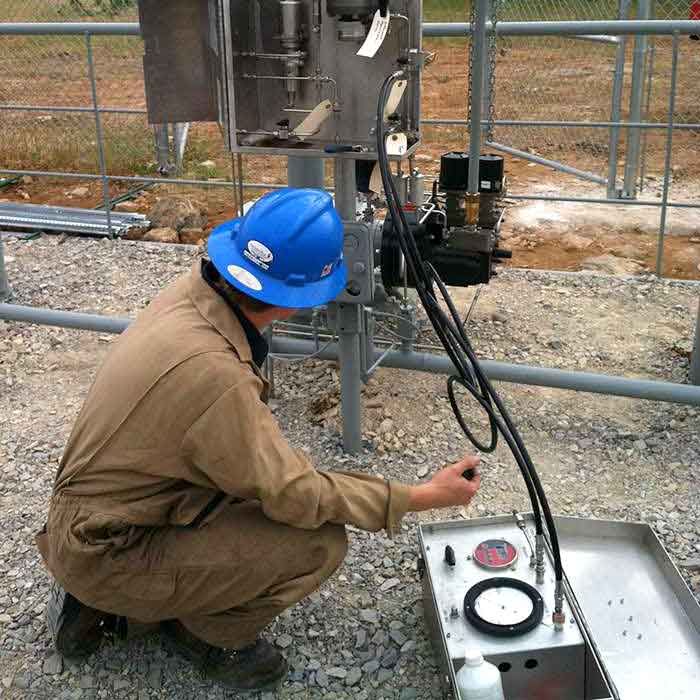
Our services include:
- Accurate line break testing
- Station bypass
- Simulation of station failure
- Pre-set rate-of-drop trip point determination
- Differential pressure compressor testing
- Calibration of high/low-pressure ESD
- Operator personnel training with ROD kits
03. On-Site Installation Services
FrontLine technicians have years of experience in valve actuator installation and service. We understand your application and can provide the needed expertise to safely mate your valve and its automation either in our facility or at the job site, whether within a plant or a remote location. Our crews work quickly and efficiently, minimizing downtime and plant shut-ins.
04. Shafer Rebuild and Replacement Kits
Cost of actuator maintenance and repair increases with the age and wear of the actuator. Retrofitting is a process of auditing old actuators and re-automating them with controls. This ensures that your plant is more efficiently controlled, and any changes due to age and wear are addressed. We offer a complete bolt-on package for name-brand actuators, while the actuator is in place, without any service interruption. We can also replace hand pumps, high-pressure controls, limit switches, and poppet blocks. If the audit shows that replacement is not necessary, we have spare kits for pumps and poppets.
05. EIM Gas Motor Rebuild and Replacement Kits
ATI/Gevalco “Gas Motor Control” packages can be used to upgrade existing EIM “G” series gas motor actuators with current, more reliable technology. The control package utilizes current “poppet” valve technology to provide reliable, maintenance-free control of gas motor actuators. The standard local “auto-manual” control consists of a “poppet” selector valve and two limit valves. The Gevalco patented limit valves, operated through a reliable cam mechanism, use a mechanical plunger integral to the proven Gevalco “poppet” valve. The “poppet” valve directly stops gas flow through the motor as opposed to operating a spool-type selector valve. This design provides quick, positive shut-off of the actuator to eliminate excessive torque on the valve and the waste of valuable gas. The “auto-manual” station, which can be remotely located, utilizes the proven and reliable Gevalco “poppet” valve design to provide a compact, easy-to-use, local control of the valve. The components can be easily field installed and calibrated to provide reliable, long-cycle life control of existing gas motor actuators.
The ATI/Gevalco Advantage
- Bubble-tight “poppet” design eliminates the seal-cutting problem associated with the existing spool valve design.
- Valve material is marine-grade, hard-anodized aluminum and stainless steel for maximum corrosion resistance and long cycle life.
- Built-in pilot pistons provide signal input from other solenoids or pneumatic devices.
- High flow exhaust shuttle valve improves motor efficiency while reducing gas consumption.
- Commercially available 3-way SS ball valve for local manual operation.
- Optional limit switches with (2) explosion-proof SPDT hermetically sealed proximity switches for remote indication.
- Optional remote electric operation with (2) 2-way explosion-proof solenoids.
- The unit comes pre-tubed for an easy bolt-on; Connect power, gas, and go.
06. On-site Repair and Start-Up Service
ATI customizes valve automation solutions to meet our customers’ specific needs. Almost 20 years ago, our story began with proprietary technology in customizing linear actuators. Those signature series actuators helped ATI build a strong reputation in the flow control industry. Paying attention to engineering specs became our core competency. Since that time, ATI has expanded our customization to include automation solutions when power is not readily available, controls for fast speeds, modulations or special conditions, and actuators for the pipeline industry. We have experienced technicians, as part of ATI FrontLine Services, to repair or provide startup for on-site installations.
ATI Machining Services
ATI has been a customized producer of high-quality valve automation products for more than 20 years. Our capabilities, including a new 41,000 square-foot air-controlled Houston area manufacturing and engineering center, are well suited for machining custom parts of any quantity, large or small. We offer turn-key design and engineering services with a team having more than 50 years of experience, using 3D CAD, Solidworks 3D modeling software, and PDM revision control. ATI is ISO 9001 certified with a quality management system that provides in-process and 100% final inspections.
Our shop is equipped with the latest CNC machines utilizing CAM software to create programs for lathes and mills.
01. CNC Milling
Machine Type | Size |
---|---|
Hyundai Kia KH80 Horizontal Machining Center | 49 x 39 X-Y TRAVEL 80 UNIT TOOL CHANGER, 4600 LB TABLE CAPACITY |
Yama Seiki BM1020 Vertical Machining Center | 40 x 23 X-Y TRAVEL 21 UNIT TOOL CHANGER |
Supermax rebel YCM-V85A | 40 x 23 X-Y TRAVEL 12 UNIT TOOL CHANGER |
02. CNC Turning
Machine Type | Size |
---|---|
You Ji YV-1200ATC+C Vertical Turning Lathe | 55 x 35 X-Z TRAVEL, C AXIS LIVE TOOLING, 12 UNIT TOOL CHANGER, 10,000 LB TABLE CAPACITY |
Feeler FT-350 Horizontal Turning Lathe | 24 x 40 X-Z TRAVEL, 3.6″ SPINDLE BORE AND 12 STATION TURRET |
Fortune VT 26 Horizontal Turning Lathe | 16 x 35 X-Z TRAVEL, 2.6″ SPINDLE BORE AND 10 TOOL STATION TURRET |
Hyundai Kia SKT-V80 RM Vertical Turning Lathe | 31 x 31 X-Z TRAVEL, 12 STATION LIVE TOOLING TURRET |
03. Manual Machines
Machine Type | Size |
---|---|
Kingston HD-2260 Horizontal Lathe | 22 x 60, 4 1/16″ SPINDLE BORE, NEW ALL DIGITAL READ OUT |
Kingston HR-2000 Horizontal Lathe | 40 x 80, 4 1/16″ SPINDLE BORE, NEW ALL DIGITAL READ OUT |
Kingston HD-2290 Horizontal Lathe | 22 x90, 4 1/16″ SPINDLE BORE, NEW ALL DIGITAL READ OUT |
Sharp 16600 Horizontal Lathe | 16 x 40, 2 1/16″ SPINDLE BORE, NEW ALL DIGITAL READ OUT |
Supermax Vertical Mill | 9 x48, NEW ALL DIGITAL READ OUT |
Enco Vertical Mill | 9 x48, NEW ALL DIGITAL READ OUT |
Summit Drill Press | 3′ Arm, 22″ Table |
04. Welding & Fabrication
Machine Type | Size |
---|---|
Miller welder Millermatic 250 | 250 AMP MIG WELDER |
Esab Migmaster 280 Pro | 300 AMP MIG WELDER |
Thermal Arc fabricator 252 I | 250 AMP MIG, STICK, AND TIG |
Wellsaw 1318 | 13 X 18 |
Acetylene Torch | |
Cutmaster Plasma cutter | 150 amp |
05. Inspection Tools
Type | Size |
---|---|
Multiple Dial/Vernier Calipers | 0-48″ Calibrated Annually |
Multiple Micrometers | 0-24″ Calibrated Annually |
Large Selection of Ring and Plug Gages | Calibrated Annually |
Depth Micrometers | 0-6″ Calibrated Annually |
I.D. Micrometers | 4-32″ Calibrated Annually |
Granted Table | 36″ X48″ Certified |
06. Cranes
Type | Size |
---|---|
Overhead Crane | 5 Ton |
Overhead Crane | 2.5 Ton |
Jib Cranes | 2 Ton |
Jib Cranes | 1/2 Ton |
Jib Cranes | 1/4 Ton |
Gorbel Crane | 2 Ton |
07. Paint & Sandblast
Type | Size |
---|---|
Paint Booth | 12’X5′ |
Empire Blast Cabinet 7272 | 36″ Turntable 3000lb Capacity |